SsangYong Rexton Service Repair Manual Chassis PDF. Repair Guide 1306 Pages. Get your hands on the complete Ssangyong factory workshop software. £9.99 Download now. SsangYong Rexton (RHD) Electrical Wiring Diagram PDF. Other Manuals 288 Pages. Undertale save file download. SsangYong OLD Rexton Service Repair Manual PDF. Repair Guide 1855 Pages. SsangYong Rexton Service Repair Manual. This manual includes procedure for maintenance, adjustment, service operation and removal and installation of components. All information, illustrations and specifications contained in this manual are based on the latest product information available at the time of manual approval. Part Description Parts Labour Total RRP Recommended Change; ELEMENT KIT-FUEL FILTER: $101.42: $39.60: $141.02: 24M or 30,000 kms: BRAKE FLUID CHANGE: $18.65: $79.20. View and Download SSANGYONG REXTON owner's manual online. SSANGYONG REXTON. REXTON automobile pdf manual download. Purpose of this is to catalog and include a comprehensive, relevant and accessible database for your Ssangyong Rexton. To get started, select the appropriate high-quality original PDF 'fix-it' manual for your Rexton, to get the problem sorted right away Ssangyong Rexton Service Repair Manual Download!!! Ssangyong Rexton Y200 2001-2006 Full Service Repair Manual Ssangyong Rexton.
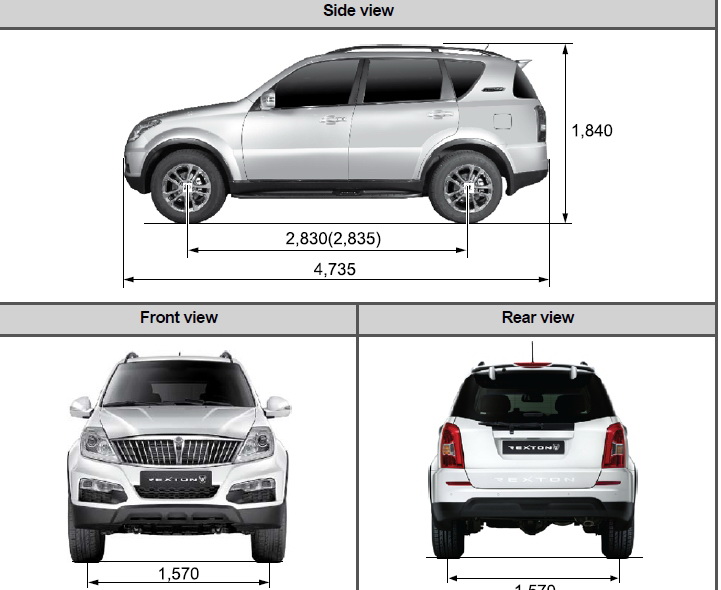
Cached

Cached
Ssangyong Rexton Owners Manual Pdf
DESCRIPTION AND OPERATION BTRA M74 4WD AUTOMATIC TRANSMISSION The BTR Automotive Model 74 Four Speed Automatic Transmission is an electronically controlled overdrive four speed unit with a lock-up torque converter. The lock-up torque converter results in lower engine speeds at cruise and eliminates unnecessary slippage. These features benefit the customer through improved fuel economy and noise reduction.
320
Max. Power (kW)
Configuration
160
260 mm Torque Converter-Wide Ratio Gear Set Splined Output for Transfer Case
Of primary significance is the Transmission Control Module (TCM) which is a microprocessor based control system. The TCM utilizes throttle position, rate of throttle opening, engine speed, vehicle speed, transmission fluid temperature, gear selector position and mode selector inputs, and in some applications a Kickdown Switch to control all shift feel and shift schedule aspects. The TCM drives a single proportional solenoid multiplexed to three regulator valves to control all shift feel aspects. The output pressure of this solenoid is controlled as a function of transmission fluid temperature to maintain consistent shift feel throughout the operating range. Shift scheduling is highly flexible, and several independent schedules are programmed depending on the vehicle. Typically the NORMAL schedule is used to maximize fuel economy and driveability, and a POWER schedule is used to maximize performance. WINTER schedule is used to facilitate starting in second gear.
KAA5A010
OPERATORS INTERFACES
•
P - Park position prevents the vehicle from rolling either forward or backward by locking the transmission output shaft. The inhibitor switch allows the engine to be started. For safety reasons, the parking should be used in addition to the park position. Do not select the Park position until the vehicle comes to a complete stop because it mechanically locks the output shaft.
•
R - Reverse allows the vehicle to be operated in a rearward direction. The inhibitor switch enables reverse lamp operation. N - Neutral allows the engine to be started and operated while driving the vehicle. The inhibitor switch
There are three operator interfaces as the following;
• • •
Gear Shift Control Lever Driving Mode Selector Indicator Light
Gear Shift Control lever The transmission uses a conventional shift control lever. The gear shift control lever can be moved from one position to another within the staggered configuration of the shift control lever gate to positively indicate the gear selection.
•
SSANGYONG Y200
AUTOMATIC TRANSMISSION 5A-3 allows the engine to be started. There is no power transferred through the transmission in Neutral. But the final drive is not locked by the parking pawl, so thewheels are free to rotate.
•
D - Overdrive range is used for all normal driving conditions. 4th gear (overdrive gear) reduces the fuel consumption and the engine noise. Engine braking is applied with reduced throttle. First to second (1 → 2), first to third (1 → 3), second to third (2 → 3), second to fourth (2 → 4), third to fourth (3 → 4), fourth to third (4 → 3), fourth to second (4 → 2), third to second (3 → 2), third to first (3 → 1) and second to first (2 → 1) shifts are all available as a function of vehicle speed, throttle position and the time change rate of the throttle position. Downshifts are available for safe passing by depress-ing the accelerator. Lockup clutch may be enabled in 3rd and 4th gears depending on vehicle type.
•
•
•
3 - Manual 3 provides three gear ratios (first through third) and prevents the transmission from operating in 4th gear. 3rd gear is used when driving on long hill roads or in heavy city traffic. Downshifts are available by depressing the accelerator. 2 - Manual 2 provides two gear ratios (first and second). It is used to provide more power when climbing hills or engine braking when driving down a steep hill or starting off on slippery roads. 1 - Manual 1 is used to provide the maximum engine braking when driving down the severe gradients.
KAA5A020
Driving Mode Selector The driving mode selector consists of a driving mode selector switch and indicator light. The driving mode selector is located on the center console and allows the driver to select the driving mode. The driving modes available to be selected vary with vehicle types. Typically the driver should have the option to select among NORMAL, POWER and WINTER modes.
SSANGYONG Y200
When NORMAL mode is selected upshifts will occur to maximize fuel economy. When POWER mode is selected, upshifts will occur to give maximum performance and the POWER mode indicator light is switched ON. When WINTER mode is selected, starting in second gear is facilitated, the WINTER mode indicator light is switched ON and the POWER mode indicator light is switched OFF.
Indicator Light The indicator light is located on the instrument panel. • Auto shift indicator light comes ON when the ignition switch ON and shows the gear shift control lever posi-tion. • POWER mode indicator light comes ON when the POWER mode is selected and when the kickdown switch is depressed. • WINTER mode indicator light comes ON when the WINTER mode is selected.
CONTROL SYSTEMS BTRA M74 4WD automatic transmission consists of two control systems. One is the electronic control system that monitors vehicle parameters and adjusts the transmission performance. Another is the hydraulic control system that implements the commands of the electronic control system commands.
ELECTRONIC CONTROL SYSTEM The electronic control system comprises of sensors, a TCM and seven solenoids. The TCM reads the inputs and activates the outputs according to values stored in Read Only Memory (ROM). The TCM controls the hydraulic control system. This control is via the hydraulic valve body, which contains seven electromagnetic solenoids. Six of the seven solenoids are used to control the line pressure, operate the shift valves and the torque converter lock-up clutch, and to turn ON and OFF the two regulator valves that control the shift feel. The seventh solenoid is the proportional or Variable Pressure Solenoid (VPS) which works with the two regulator valves to control shift feel. Transmission Control Module (TCM) The TCM is an in-vehicle micro-processor based transmission management system. It is mounted under the driver's side front seat in the vehicle cabin. The TCM contains: • Processing logic circuits which include a central microprocessor controller and a back-up memory system. • Input circuits.
5A-4 AUTOMATIC TRANSMISSION
•
Output circuits which control external devices such as the Variable Pressure Solenoid (VPS) driver, On/ Off solenoid drivers, a diagnostics output and the driving mode indicator light.
Processing Logic Shift schedule and calibration information is stored in an Erasable Programmable Read Only Memory (EPROM). Throttle input calibration constants and the diagnostics information are stored in Electrically Erasable Programmable Read Only Memory (EEPROM) that retains the memory even when power to the TCM is disconnected. TCM continuously monitors the input values and uses these, via the shift schedule, to determine the required gear state. At the same time it monitors, via the solenoid outputs, the current gear state, whenever the input conditions change such that the required gear state is different to the current gear state, the TCM initiates a gear shift to bring the two states back into line. Once the TCM has determined the type of gearshift required the TCM accesses the shift logic, estimates
the engine torque output, adjusts the variable pressure solenoid ramp pressure then executes the shift. The TCM continuously monitors every input and output circuit for short or open circuits and operating range. When a failure or abnormal operation is detected the TCM records the condition code in the diagnostics memory and implements a Limp Home Mode (LHM). The actual limp home mode used depends upon the fail-ure detected with the object to maintain maximum drive-ability without damaging the transmission. In general input failures are handled by providing a default value. Output failures, which are capable of damaging the transmission, result in full limp mode giving only third or fourth gear and reverse. For further details of limp modes and memory retention refer to the Diagnostic Trouble Code Diagnosis Section. The TCM is designed to operate at ambient temperatures between - 40 and 85 °C (- 40 and 185 °F). It is also protected against electrical noise and voltage spikes, however all the usual precautions should be observed, for example when arc welding or jump starting.
KAA5A030
TCM Inputs To function correctly, the TCM requires engine speed, vehicle speed, transmission fluid temperature, throttle position, gear position and Kickdown Switch inputs to determine the variable pressure solenoid current ramp
and on/off solenoid states. This ensures the correct gear selection and shift feel for all driving conditions. The inputs required by the TCM are as follows;
SSANGYONG Y200
AUTOMATIC TRANSMISSION 5A-5
•
•
•
Engine Speed The engine speed signal is derived from the Controller Area Network (CAN) via Engine Control Module (ECM). Vehicle Speed The vehicle speed sensor, which is located in the transfer case, sends the output shaft speed signal to the Engine Control Module (ECM). The information is then transferred to the TCM via the CAN. Transmission Fluid Temperature The transmission fluid temperature sensor is a thermistor located in the solenoid wiring loom within the valve body of the transmission. This sensor is a typical Negative Temperature Coefficient (NTC) resistor with low temperatures producing a high resistance and high temperatures producing a low resistance. If the transmission fluid temperature exceeds 135 ° C (275 ° F), the TCM will impose converter lock-up at lower vehicle speeds and in some vehicles flashes the mode indicator light. This results in maximum oil flow through the external oil cooler and eliminates slippage in the torque converter. Both these actions combine to reduce the oil temperature in the transmission. Temperature
Pin No. Codes and colors in Solenoid Loom Pin No.
Wire Color
Connects to
1
Red
Solenoid 1
2
Blue
Solenoid 2
3
Yellow
Solenoid 3
4
Orange
Solenoid 4
5
Green
Solenoid 5
6
Violet
Solenoid 6
7
Brown
Solenoid 7
8
Green
Solenoid 5
9
White
Temperature Sensor
10
Red
Temperature Sensor
Resistance (Ohms)
(°C)
Minimum
Maximum
-20
13,638
17,287
0
5,177
6,616
Throttle Position Sensor
20
2,278
2, 723
100 135 (Overheat Mode Threshold)
117
196
75
85
Gasoline Engine: The throttle position signal is sent from the ECM to the TCM via the CAN. Refer to Engine Section for further details.
KAA5A040
SSANGYONG Y200
KAA5A050
Diesel Engine: The throttle position sensor(TPS) is a resistance potentiometer which is installed on the injection pump. It transmits a signal to the TCU proportional to the throttle plate opening. The potentiometer is connected to the TCU by three wires: 5 volts positive supply, earth and variable wiper voltage. Throttle voltage adjustments are as follows: • Closed throttle voltage is 0.2 V to 1.0 V. • Wide open throttle voltage is 3 V to 4.5 V. These measurements are taken between pins 1 and 3 of the TPS connentor.
5A-6 AUTOMATIC TRANSMISSION Maintaining good shift feel through the transmission life span is dependant on having an accurate measure of the engine throttle position. To achieve this the TCU continuously monitors the maximum and minimum throttle potentiometer voltages and, if a change occurs, stores the new voltage values. However these limits will be lost and will require relearning should a new TCU be installed, or the throttle calibration data is cleared by the execution of a particular sequence. This last instance depends on the installation, and reference should be made to the Diagnostics Section of this manual. The relearning will happen automatically.
YAD5A250
Gear Position Sensor The gear position sensor is incorporated in the inhibitor switch mounted on the side of the transmission case.
KAA5A060
The gear position sensor is a multi-function switch providing three functions;
• • •
Inhibit starting of the vehicle when the shift lever is in a position other than Park or Neutral Illuminate the reverse lamps when Reverse is selected
Readings for Resistance / Shift Lever Positions Shift Lever Position
Ω) Resistance (kΩ
Manual 1
1 ~ 1.4
Manual 2
21.8 ~ 2.2
Manual 3
3 3 ~ 3.4
Drive
4.5 ~ 4.9
Neutral
6.8 ~ 7.2
Reverse
10.8 ~ 11.2
Park
18.6 ~ 19
Kickdown Switch The Kickdown Switch is used to signal the TCM that the driver has pressed the acclerator to the floor and requires a kickdown shift. When this switch is used, the POWER light comes ON and the POWER shift pattern is used. Diagnostic Inputs The diagnostic control input or K-line is used to initiate the outputting of diagnostic data from the TCM to a diagnostic test instrument. This input may also be used to clear the stored fault history data from the TCM's retentive memory. Connection to the diagnostic input of the TCM is via a connector included in the vehicle's wiring harness or computer interface. Battery Voltage Monitoring Input The battery voltage monitoring input is connected to the positive side of the battery. This signal is taken from the main supply to the TCM. If the battery voltage at the TCM falls below 11.3 V, the transmission will adopt a low voltage mode of operating in which shifts into first gear are inhibited. All other shifts are allowed but may not occur because of the reduced voltage. This condition normally occurs only when the battery is in poor condition. If the battery voltage is greater than 16.5 V, the transmission will adopt limp home mode and all solenoids are turned OFF. When system voltage recovers, the TCM will resume normal operation after a 30 seconds delay period. TCM Outputs The outputs from the TCM are supplied to the components described below; • Solenoids • Mode Indicator Light
Indicate to the TCM which lever position has been selected by way of a varying resistance.
SSANGYONG Y200
AUTOMATIC TRANSMISSION 5A-7 Solenoids The TCM controls seven solenoids. Solenoids 1 to 6 (S1 to S6) are mounted in the valve body, while Solenoid 7 (S7) is mounted in the pump cover. • Solenoid 1 and 2: S1 and S2 are normally open ON/ OFF solenoids that set the selected gear. These solenoids determine static gear position by operating the shift valves. Note that S1 and S2 solenoids also send signal pressure to allow or prohibit rear band engagement. • Solenoid 3 and 4: S3 and S4 are normally open ON/ OFF solenoids that combine to control shift quality and sequencing. S3 switches the clutch regulator valve OFF or ON. S4 switches the front band regulator valve OFF or ON. S5 also provides the signal pressure for the converter clutch regulator valve.
•
Solenoid 5: S5 is a variable pressure solenoid that ramps the pressure during gear changes. This solenoid provides the signal pressure to the clutch and band regulator, thereby controlling the shift pressures. S5 also provides the signal pressure for the converter clutch regulator valve.
SSANGYONG Y200
•
Solenoid 6: S6 is a normally open ON/OFF solenoid that sets the high/low level of line pressure. Solenoid OFF gives high pressure. • Solenoid 7: S7 is a normally open ON/OFF solenoid that controls the application of the converter clutch. Solenoid ON activates the clutch. Solenoid Logic for Static Gear States Gear
S1
S2
1st
ON
ON
2nd
OFF
ON
3rd
OFF
OFF
4th
ON
OFF
Reverse
OFF
OFF
Neutral
OFF
OFF
Park
OFF
OFF
5A-8 AUTOMATIC TRANSMISSION Solenoid Operation during Gearshifts Shift
To Initiate Shift
Typical S5 Current Ramp
To Complete Shift
1-2
S1 OFF
750mA to 600mA
S4 OFF
850mA to 750mA
S4 OFF
S4 ON 1-3
S1 OFF S2 OFF
S3 OFF
S3 ON S4 ON 1-4
S2 OFF S3 ON
S3 OFF 850mA to 750mA
S4 OFF
700mA to 500mA
S3 OFF
S4 ON 2-3
S2 OFF S3 ON
S4 OFF
S4 ON 3-4
S1 ON
750mA to 600mA
S4 OFF
750mA to 900mA
S1 OFF
S4 ON 4-3
S4 ON
S4 OFF 4-2
S3 ON
S1 OFF 750mA to 950mA
S2 ON S3 OFF
4-1
S3 ON S4 ON
S2 ON 600mA to 1000mA
S3 OFF S4 OFF
3-2
S2 ON S4 ON
S4 OFF 600mA to 450mA @ 20 kph. 550mA to 400mA @ 60 kph. 800mA to 650mA @ 100 kph.
3-1
S3 ON
S1 ON
S4 ON
S2 ON S3 OFF
2-1
S4 ON
700mA to 950mA
S4 OFF
800mA to 950mA
S1 ON S4 OFF
Conv. Clutch ON
S7 ON
OFF
700mA to 400mA
S7 OFF
600mA to 100mA
SSANGYONG Y200
AUTOMATIC TRANSMISSION 5A-9 Solenoid Valve Symbols (ON/OFF Solenoids) The solenoid symbol shown adjacent to each solenoid on the hydraulic system schematics indicates the state of the oil flow through the solenoid valve with the power ON or OFF. Normally Open (NO) Solenoid POWER ON: Line 500 port is closed. The output port is open to exhaust at the solenoid valve. POWER OFF: The exhaust port is closed. The output port is open to line 500.
This applies full Line 500 pressure to the plunger and because Line 500 pressure is always greater than S5 pressure it squeezes the S5 oil out between the regulator valve and the plunger. The friction elements are then fed oil pressure equal to Line 500 multiplied by the amplification ratio. When a shift is initiated the required ON/OFF solenoid is switched ON cutting the supply of Line 500 to the plunger. At the same time the VPS pressure is reduced to the ramp start value and assumes control of the regulator valve by pushing the plunger away from the valve. The VPS then carries out the required pressure ramp and the timed shift is completed by switching OFF the ON/ OFF solenoid and returning the VPS to the standby pressure. This system enables either the band or clutch or both to be electrically controlled for each gearshift. Mode Indicator Light Depending on the application, the mode indicator light may be used to indicate the mode that has been selected or if an overheat condition exists. The mode indicator light is usually located on the instrument cluster.
KAA5A070
Variable Pressure Solenoid Multiplexing System Friction element shifting pressures are controlled by the Variable Pressure Solenoid (VPS). Line pressure is completely independent of shift pressure and is a function of throttle position, gear state and engine speed. S5 is a proportional or variable pressure solenoid that provides the signal pressure to the clutch and band regulator valves thereby controlling shift pressures. VPS pressure is multiplexed to the clutch regulator valve, the band regulator valve and the converter clutch regulator valve during automatic gearshifts. A variable pressure solenoid produces a hydraulic pressure inversely proportional to the current applied. During a gearshift the TCM applies a progressively increasing or decreasing (ramped) current to the solenoid. Current applied will vary between a minimum oaf 200 mA and a maximum of 1000 mA. Increasing current decreases output (S5) pressure. Decreasing current increases output (S5) pressure. Line 500 pressure, (approximately 440 to 560 kPa), is the reference pressure for the VPS, and the VPS output pressure is always below line 500 pressure. When the VPS is at standby, that is no gearshift is taking place, the VPS current is set to 200 mA giving maximum output pressure. Under steady state conditions the band and clutch regulator valve solenoids are switched OFF.
SSANGYONG Y200
Communication Systems CAN The Controller Area Network (CAN) connects various control modules by using a twisted pair of wires, to share common information. This results in a reduction of sensors and wiring. TCM obtains the actual engine speed and throttle position, vehicle speed and accelerator position etc. from ECM via CAN without any additional sensors. K-Line The K-line is typically used for obtaining diagnostic information from the TCM. A scan tool with a special interface is connected to the TCM via Data Link Connector (DLC) and all current faults, stored faults, runtime parameters are then available. The stored trouble codes can also be cleared by scan tool. The K-line can be used for vehicle coding at the manufacturer's plant or in the workshop. This allows for one TCM design to be used over different vehicle mod-els. The particular code is sent to the microprocessor via the K-line and this results in the software selecting the correct shift and VPS ramp parameters. Data Link Connector (DLC) The Data Link Connector (DLC) is a multiple cavity connector. The DLC provides the means to access the serial data from the TCM. The DLC allows the technician to use a scan tool to monitor the various systems and display the Diagnostic Trouble Codes (DTCs).
5A-10 AUTOMATIC TRANSMISSION The DLC connector is located within the driver's compartment, directly below the instrument panel on the driver's side.
The pump cover contains the following; • Primary regulator valve for line pressure • Converter clutch regulator valve
• •
A103A321
HYDRAULIC CONTROL SYSTEM The hydraulic controls are located in the valve body, pump body and main case. The valve body contains the following; • Manual valve • Three shift valves • Sequence valve • Solenoid supply pressure regulator valve • Line pressure control valve • Clutch apply feed regulator valve • Band apply feed regulator valve • Solenoid S1 to S6 • Reverse lockout valve
Converter clutch control valve Solenoid S7 The main case contains the following; • B1R exhaust valve All upshifts are accomplished by simultaneously switching on a shift valve(s), switching VPS pressure to the band and/or clutch regulator valve, and then sending the VPS a ramped current. The shift is completed by switching the regulators OFF and at the same time causing the VPS to reach maximum pressure. All downshifts are accomplished by switching VPS pressure to the band and/or clutch regulator valve and sending a ramped current to the VPS. The shift is completed by simultaneously switching the regulators OFF, switching the shift valves and at the same time causing the VPS to return to stand-by pressure. The primary regulator valve is located in the pump cover and supplies four line pressures; high and low for forward gears, and high and low for reverse. This pressure has no effect on shift quality and merely provides static clutch capacity during steady state operation. Low pressure can be obtained by activating an ON/OFF solenoid with high line pressure being the default mode. Torque converter lock-up is initiated by toggling the converter clutch control valve with an ON/OFF solenoid. The actual apply and release of the clutch is regulated by the VPS via the converter clutch regulator valve. The solenoid supply pressure regulator valve provides reference pressure for all the solenoids.
SSANGYONG Y200